What is Conednsate Recovery?
With Steam Generation as a Prerequisite
A condensate recovery unit is a device used to collect, treat and reuse condensate from industrial or commercial steam systems. It reintroduces high-temperature condensate generated from the cooling of steam into the heating system or production process, thereby realizing energy savings, reducing water waste, and lowering operating costs.
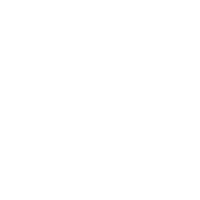
Sources of Condensate
Condensate is the product of the conversion of steam to liquid water after cooling during heat exchange or piping. It usually has the following characteristics:
1. High temperature: The temperature of condensate is usually close to the temperature of steam (80-120°C).
2. Good water quality: Since the steam is purified before condensation, condensate usually has a low hardness and impurity content.
The principle of operation of a condensate recovery unit is shown in Figures 1 and 2.
1. Collection: The steam condensate recovery unit separates the condensate discharged from the steam equipment by means of a trap and conveys it to a collection tank.
2. Conveying: The steam is separated from the water using a vapor separation device. The high-temperature condensate is then pumped directly back to the boiler or heat exchange system through a fully automated control system, thus forming a closed loop from steam supply to recovery.
3. Treatment: The collected condensate is filtered and purified to remove contaminants, then stored and sterilized to ensure safe water quality.
4. Reuse: The treated condensate is sent back through pressurized or gravity flow for use as boiler make-up water, cooling system make-up water, or other production water.
Composition of condensate recovery device
1. Collection system: condensate piping, water collection tank.
2. Filtering equipment: removing impurities in the condensate, such as particles or oil.
3. Pressurizing pump: transfer condensate to boiler or other equipment.
4. Control systems: monitor and regulate the flow, temperature and pressure of the condensate.
Condensate Recovery Direction
1. Boiler make-up water
Boiler water temperature needs to be heated to produce steam. The temperature of condensate is high, and reuse can reduce the fuel needed to heat the boiler.
2. Process water
Process equipment, such as heat exchangers, condensate is used as a heat medium or water source. In addition, in some process industries, condensate is used for equipment cleaning, sterilization, pharmaceutical production, and high temperature water.
3. Thermal energy utilization
Recycling in building heating or centralized heating, cooling water is recovered and used as boiler make-up water and preheating. Similarly, the use of condensate recovery for hot water supply in large buildings, hotels and hospitals can realize energy recycling.
4. Cooling water system
As part of the cooling medium, it directly reduces the heat generated by production to protect the equipment.
5. Waste water reuse system
The condensate from steam is reused at a location specified by the user, such as for irrigation, cleaning or cooling tower replenishment.
Advantages of Condensate Recovery
1. Energy Savings: Reduces boiler fuel and other heating energy consumption. According to the principle of boiler operation and steam recovery, for every 6°C increase in boiler feedwater temperature, about 1% of boiler fuel can be saved. As shown in Figure 3, steam condensate reused at higher temperatures (80°C-120°C) can save 20% and more of fuel.
2. Water Conservation: Reduces the need for fresh water. As shown in Figure 4, water savings can exceed 80%.
3. Reduced operating costs: Reduces boiler water and fuel consumption. Reduced water treatment costs and boiler maintenance costs (better water quality, equipment less prone to scaling and corrosion).
4. Environmental benefits: Reduced wastewater discharge and thermal pollution.
Note: Natural gas can be exchanged for other types of energy to compare
Typical Application Areas
1. Industrial areas:
- Power plants, petrochemical plants, pharmaceutical plants, food processing plants and other industries that require large amounts of steam.
2. Commercial field:
- Hotels, hospitals, centralized heating systems and other places that require steam for heating or hot water.
3. Others:
- Washing industry, paper mills, textile mills, etc.